Investigation on Dynamic Performance of Aluminium – Steel Composite Foam based Redundant SCARA Robot
DOI:
https://doi.org/10.63746/njtd.v22i3.3023Keywords:
Aluminium alloy-A356, Al-LC steel composite foam, Redundant SCARA, MATLAB, Simscape Multibody, Dynamic propertyAbstract
This research examines the effects of foam made of aluminium alloy low carbon (Al-LC) steel on the joint dynamics of Redundant Selective Compliance Articulated Robot Arm (RSCARA). When building a SolidWorks CAD model that incorporates MATLAB/Simscape Multibody, RSCARA components are designed using a customized composite foam material. The dynamic property torque generated at robot joints is determined by simulating the RSCARA system blocks technique using the Simscape Multibody System (SMBS). The use of Aluminium-Low Carbon Composite Metal Foam (AL-LC CMF) in the evolution of RSCARA was shown to be relevant by the dynamic property observations based on the Simscape simulation results.
References
Agbo, D. O., Enokela, J. A., & Goshwe, Y. N. (2021). Design and Simulation of a Walking Biped Robot using MATLAB/Simscape/Multibody. Indian Journal of Engineering, 18(49), 31-39.
Alshamasin M. S., Ionesco F, AL-Kasasbeh R.T (2012), Kinematic Modelling and Simulation of a SCARA Robot by using Solid Dynamics and Verification by Matlab/Simulink”, Int. J. Model. Identif. Control, 15 (1), 28-38
Ashby M.F., Evans A, Fleck N.A, Gibson L.J, Hutchinson J.W (2000), Metal Foams: A Design Guide, Butterworth- Heinemann, Wolburn, MA.., 2000.
Boschetti, G., & Sinico, T. (2024). Designing Digital Twins of Robots Using Simscape Multibody. Robotics, 13(4), 62.
Brown J. A., Lakshmi J, Vendra L.J, Rabiei A (2010), Bending Properties of Al-Steel and Steel-Steel Composite Metal Foams, Metall. Mater. Trans. A, 41, 2010, 2784-93.
Bruzzone, L., Verotti, M., & Fanghella, P. (2024). Exploiting the Natural Motion of a SCARA-Like Manipulator for Pick-and-Place Tasks. In European Conference on Mechanism Science (pp. 136-143). Cham: Springer Nature Switzerland.
Crenganis, M., Barsan, A., Tera, M., & Chicea, A. (2021). Dynamic analysis of a five degree of freedom robotic arm using MATLAB-Simulink Simscape. In MATEC Web of Conferences (Vol. 343, p. 08004). EDP Sciences.
Degischer H. P., B. Kriszt (2002), Handbook of Cellular metals, Production, Processing, Applications, Wiley-VCH, Verlag.
Delikta?, D., Akta?, R., ?lgen, S., & Gülbahçe, E. (2023). Performance Evaluation of a SCARA Robot Manipulator for Trajectory Tracking Based on Error Criteria Minimization. In 2023 7th International Symposium on Innovative Approaches in Smart Technologies (ISAS) (pp. 1-5). IEEE.
Donald R. Dentler II (2008), Design, Control and Implementation of a Three Link Articulated Robot Arm, Master's thesis, Dept. Mechanical. Eng. Akron (OH), The University of Akron.
Fedak V., Durovsky F (2014), Robert Uveges In: MATLAB Applications for the Practical Engineer (ed. K. Bennett), London, Intech Open, 565-581.
Fisseha Zewdie, Alok Srivastava, Rajesh Punia, Naresh Bhatnagar (2024), Experimental investigation on the development of hybrid composite metal foam reinforced with steel hollow spheres for higher energy absorption applications, Journal of Manufacturing Processes, Volume 123, 2024, Pages 60-82,
Gang, L. S., Wang D.H, Cheng W.S, Nan Z.Y (2010), Path planning and system Simulation for an industrial spot-welding robot based on SimMechanics, Key Eng. Mater. 419, 2010, 665-668.
Gao, J., Wang Y, Chen Z (2014), Modelling and Simulation of inverse kinematics for planar 3-RRR parallel robot based on SimMechanics, Adv. Mat. Res. 898, 510-513.
Gouasmi, M., Ouali M, Fernini B, Meghatria M (2012), Kinematic modelling and Simulation of a 2-R Robot using SolidWorks and verification by MATLAB/Simulink, Int. J. Adv. Robot. Syst. 9 (6), 245-258.
Hanchen, L., Xinhua Z, Haoliang X (2009), Modelling and Simulation of 3RRRT parallel manipulator based on MALTAB with SimMechanics, International forum on Information Technology and Applications (IFITA), 290-293.
Kiyoto I, Hitonobu K, Katsuyuki K and Kenji K (2013), “Observation of Wear Surface between pure PEEK and counterpart materials; Titanium and 7075 aluminium alloy, in Robot Joint,” App. Mech. Mater. 307, 347-351.
Kupp D.M., Claar T.D, Stephani G, Waag U (2001), Fabrication of Ti-based components with controlled porosity, In: Proceedings of the International Conference on Powder Metallurgy & Particulate Materials, 2001, 50-58, New Orleans, Princeton.
Lakshmi J., Vendra L.J, Rabiei A (2007), A study on aluminium-steel composite metal foam processed by casting, Mater. Sci. Eng. A, 465, 59–67.
Lim T. J., Smith B, Mcdowell D.L (2002), Behavior of a random hollow sphere metal foam, Acta. Mater., 50, 2867–79.
Mahadev Madgule, Sreenivasa C.G, Avinash V Borgaonkar (2023), Aluminium metal foam production methods, properties and applications- a review, Materials Today: Proceedings, Volume 77, Part 3, Pages 673-679, ISSN 2214-7853.
Mashagbeh M. A., Khamesee M. B (2015), Virtual Performance Evaluation of an Industrial SCARA Robot Prior to Real-World Task, Microsyst. Technol., 21(12), 2605–2609.
Matoui, F., Boussaid B, Abdelkrim M. N (2018), Distributed path planning of a multi-robot system based on the neighborhood artificial potential field approach, Simulation 95(7), 637-657.
Mezui, J. M. L. N., Moungomo, J. B. M., Kibouka, G. R., Okou, F., & Saad, M. (2023). SolidWorks/Simscape multibody co-simulation of the dynamic model of a mobile manipulator system. International Journal of Research in Engineering, Science and Management, 6(1), 79-87.
Mrak, B., Singh, T., Docquier, Q., & Gilis, J. (2023). Model Predictive Control of a Highly Dynamic Parallel SCARA Robot. In 2023 9th International Conference on Control, Decision and Information Technologies (CoDIT) (pp. 2027-2031). IEEE.
Neville B.P., Rabiei A (2008), Composite metal foams processed through powder metallurgy, Mater. Des., 29, 2008, 388–96.
Patel R., Shadpey F (2005), Control of Redundant Robot Manipulators, Berlin Heidelberg, Springer Verlag.
Petrov P. (2018), Dynamics and adaptive motion control of a two-wheeled inverted pendulum robot, Comptes rendus de l'Acad'emie bulgare des Sciences, 71(7), 945-954.
Rabiei, A., Vendra L.J (2009), Comparison of composite metal foam's properties and other comparable metal foams, Mater. Lett., 63, 533-536.
Saravana Mohan, M., Samuel Ratna Kumar, P.S., Mashinini, P.M., Aziz, K. (2023), Aluminium–Steel Composite Foam in Joint Dynamic Performance of Redundant Articulated Robot Components. In: Rajkumar, K., Jayamani, E., Ramkumar, P. (eds) Recent Advances in Materials Technologies. Lecture Notes in Mechanical Engineering. Springer, Singapore, 2023.
Sugimura Y., Meyer J, He M.Y, Bart-Smith H, Grenstedt J (1997), On the mechanical performance of closed cell Al alloy foams, Acta. Mater. 45, 1997, 5245–5259.
Thong Duc Hong, Minh Quang Pham, Son Cong Tran, Lam Quang Tran, Truong Thanh Nguyen (2024), A Comparative Study on Kinetics and Dynamics of Two Dump Truck Lifting Mechanisms Using MATLAB Simscape, Theoretical and Applied Mechanics Letters, 1-28.
Udai, D., Rajeevalochana C.G, Saha S.K (2011), Dynamic Simulation of a KUKA KR5 industrial robot using MATLAB SimMechanics, National Conference on Machines and Mechanisms, 1-8.
Uk, M., Ali Shah F, Soyaslan M, Eldogan O (2020), Modelling, Control, and Simulation of a SCARA PRR-type robot manipulator. Sci. Iran., 27(1), 330-340.
Urrea C., Kern J (2015), Trajectory Tracking Control of a Real, Redundant Manipulator of the SCARA Type, J. Electr. Eng .Technol. 10, 2015, 710-720.
Yu, Y., Zhang L, Zhang N, Yang S, Wang D (2010), Kinematics, Simulation and analysis of 3-RPS parallel robot on SimMechanics, IEEE International Conference on Information and Automation, 2363-2367.
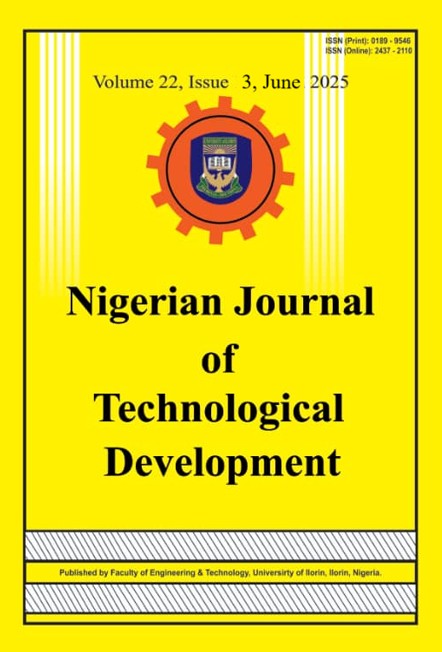
Published
Issue
Section
License
Copyright (c) 2025 Nigerian Journal of Technological Development

This work is licensed under a Creative Commons Attribution-NonCommercial-ShareAlike 4.0 International License.
In accordance with the Copyright Act of 1976, which became effective January 1, 1978, the following statement signed by each author must accompany the manuscript submitted: "I, the undersigned author, transfer all copyright ownership of the manuscript referenced above to the Nigerian Journal of Technological Development, in the event the work is published. I warrant that the article is original, does not infringe upon any copyright or other proprietary right of any third party, is not under consideration by another journal, and has not been published previously. I have reviewed and approve the submitted version of the manuscript and agree to its publication in the Nigerian Journal of Technological Development." A copyright transfer form should be downloaded from the NJTD Website ( http://njtd.com.ng/index.php/njtd). Author(s) will be consulted, whenever possible, regarding republication of material. All authors must have access to the data presented and the authors and sponsor (if applicable) must agree to share original data with the editor if requested.