Pouring Height Effects on Macro-Segregation and Electrical/Thermal Properties of Aluminium-Zinc Alloy
DOI:
https://doi.org/10.63746/njtd.v22i1.2710Keywords:
Aluminum-Zinc Alloy, Pouring Height, Macro-segregation, Microstructural Analysis, Thermal Conductivity, Electrical ConductivityAbstract
This paper investigated the effects of pouring heights on macro-segregation, electrical and thermal conductivity of an Aluminium–Zinc alloy. Al 5wt.% Zn was cast at pouring heights ranging from 100 to 500 mm. Analytical techniques like optical scanning electron and energy dispersive spectrometry were used to assess the extent of segregation. The electrical and thermal conductivities were estimated, utilising the Wiedemann-Franz Law. The thermal profile of the as-cast Al-5wt.% Zn revealed variations in solidus and liquidus reaction temperatures relative to position, attributed to local chemical composition variation and cooling rate. Notably, at a pouring height of 400 mm, the temperature field in the melt was more uniform, leading to enhanced melt flow motion and transformation of large primary α-Al grains into finer spherical grains, resulting in a more homogeneous microstructure. As a result, the Al-5wt.% Zn sample obtained at a pouring height of 400 mm exhibited the highest electrical and thermal conductivities (37 IACS and 133 W/mK), aligning well with established standards (33.8% IACS and 131 W/mK). Significantly, the magnitude of macro-segregation recorded at various pouring heights even at low concentrations of solute (5wt.% Zn) signifies that macro-segregation is strongly dependent on the process parameter (i.e., pouring height) and not just the solute concentration.
References
Guan, J.; Z.P. Pu; S.C. Zhao and D.R. Liu. (2022). Three-Dimensional Modeling of Segregation Behavior during Solidification of a Sn-6 wt.% Pb Alloy. Materials (Basel). 15 (4):1298.
Benmaziane, S.; O. Ben lenda; L. Zerrouk and E. Saad. (2021). Numerical Modelling of Copper Macro-segregation in the Binary Alloy Al-4Cu E3S Web of Conferences 229, 01015 (2021). ICCSRE’2020.
Obiekea, V.D.; I.O. Sekunowo; M.G. Sobamowo and S.O. Adeosun. (2018). Effects of Casting Speed and Runner Angle on Macro-segregation of Aluminium-Copper Alloy, JCAMECH. 49(2): 373-379.
Muhrat, A. (2022). Ultrasound-Assisted Low-Temperature Brazing of Titanium/Titanium Joints Using Aluminium Filler Alloys. Cross Ref.
Ghosh, A. (2001). Segregation in Cast Products. Sadhana, 26: 5–24.
Fernando P.Q.; J.L. Wysllan; G.P. Késsia; C. S. Roberto; A.S.B. Luis, and A. F. Ferreiraa. (2020). An Experimental Investigation of Continuous Casting Process: Effect of Pouring Temperatures on the Macro-segregation and Macrostructure in Steel Slab. Materials Research. 23 (4): e20200023.
Cameron, B.; S. Shi; E. Mark; N. Orchowski; N. Matthews, and M. Brandt. (2018). Influence of Macro-segregation on Solidification Cracking in Laser Clad Ultra-High Strength Steels. Surface and Coatings Technology. 340. 10.1016/j.surfcoat.2018.02.052.
Ali, N.; L. Zhang; H. Zhou; A. Zhao; C. Zhang; K. Fu, and J. Cheng. (2021). Investigation on Internal Crack Defects in Medium Carbon Steel by Soft Reduction. Materials Research. 24: 10.1590/1980-5373-MR-2021-0055.
Chouhan, A.; M. Hesselmann; A. Toenje; L. Mädler and N. Ellendt. (2022). Numerical Modelling of In-Situ Alloying of Al and Cu Using the Laser Powder Bed Fusion Process: A Study on the Effect of Energy Density and Remelting on Deposited Track Homogeneity, Additive Manufacturing. 59:
Munekazu, O.; Y. Masayoshi and M. Kiyotaka. (2019). Importance of Microstructural Evolution on Prediction Accuracy of Micro segregation in Al-Cu and Fe-Mn Alloys, International Journal of Heat and Mass Transfer, 132: 1004-1017.
Zhang, Y.; X. Liu; Q. Zhu; Y. Zuo; R. Wang and H. Jiang. (2024). Understanding of Macro-Segregation in Direct-Chill Cast 2024 Alloy with Intensive Melt Shearing Based on the Evolution of Microstructure and Temperature Field, Journal of Materials Research and Technology. 27: 7766-7777.
Marchwica, P. (2012). Microstructural and Thermal Analysis of Aluminium-Silicon and Magnesium-Aluminium Alloys Subjected to High Cooling Rates, Electronic Thesis and Dissertations, University of Windsor.
Clemens, J.M. (2000). How Thermal conductivity relates to electrical conductivity. Technical Data, Test & Measurement 6 (2):1-6.
Wei, C.; N. Antolin; O.D. Restrepo; W. Windl and J. Zhao. (2017). A General Model for Thermal and Electrical Conductivity of Binary Metallic Systems, Acta Materialia. 126 (7):272-279
Devanathan, V. (2021). The Wiedemann-Franz Law for Electrical and Thermal Conduction in Metals. 4: 1-26.
Ordonez-Miranda, J. and J.J. Alvarado-Gil. (2012). Thermal Conductivity of Nanocomposites with High Volume Fractions of Particles. Composites Science and Technology. 72 (7): 853-857.
Volklein, F.; H. Reith; T.W. Cornelius and M. Rauber (2009). The experimental investigation of thermal conductivity and the Wiedemann–Franz law for single metallic nanowires. IOP Science, Nanotechnology. 20 (32): 1-8.
Obiekea, V.D.; I.O. Sekunowo, M.G. Sobamowo, and S.O. Adeosun. (2018). Study of macro-segregation effects on thermal and electrical characteristics of aluminium-copper alloy. ACTA TECHNICA CORVINIENSIS – Bulletin of Engineering. 3:35-38.
Liu, Y.; M. Liu; L. Luo; J. Wang, and C. Liu (2014). The solidification behaviour of AA2618 aluminium alloy and the influence of cooling rate. Material. 7: 7875-7890.
Rominiyi, A.L; D. Isadare; M. Adeoye; K. Akinluwade and A. Adetunji. (2015). Effect of As-Cast Cooling on the Microstructure and Mechanical Properties of Age-Hardened 7000 Series Aluminium Alloy. International Journal of Materials Engineering, 5 (1): 5-9
Li, Y; W. Chen and Y. Sun. (2023). Analysis of macro-segregation during slab continuous casting using a 3D-longitudinal 2D hybrid model. Ironmaking and Steelmaking. 50 (7): 794-808. doi:10.1080/03019233.2023.2190255
Riahi, D.N. (2002). Effects of Rotation on Convection in a Porous Layer During Alloy SolidificationTransport Phenomena in Porous Media II, book.
Galenko, P.K.; D.A. Danilov; K. Reuther; D.V. Alexandrov; M. Rettenmayr and D.M. Herlach. (2017). Effect of convective flow on stable dendritic growth in rapid solidification of a binary alloy. Journal of Crystal Growth. 457 (1): 349-355.
Malakhov, V.; P. Dmitri; G. Damon and M Mark. (2010). On the formation of intermetallics in rapidly solidifying Al–Fe–Si alloys. Calphad. 34 (2): 159-166.
Mrówka-Nowotnik G.; J. Sieniawski, and M. Wierzbiñska. (2007). Intermetallic-phase-particles-6082-aluminium-alloy, Archives of Material Science and Engineering. 2 (28): 69 – 76.
Adam, W.L. (2005). Predicting The Thermal Conductivity of Aluminium Alloys in the Cryogenic to Room Temperature Range, Journal of Engineering and Apply Science. 45: 421–431
Zhang D. and J. Wang. (2015). Thermal Conductivity Prediction of Closed-Cell Aluminium Alloy Considering icropore Effect. Advances in Mechanical Engineering. 1–8.
Payandeh, M.; E. Sjölander; A. E. W. Jarfors, and M. Wessén. (2016). Influence of Microstructure and Heat Treatment on Thermal Conductivity of Rheocast and Liquid Die Cast Al-6Si-2Cu-Zn Alloy, International Journal of Cast Metals Research. 29 (4): 202-213.
Ikumapayi, O.M.; E.T. Akinlabi and J.D. Majumdar. (2018). Review on Thermal, Thermo-Mechanical and Thermal Stress Distribution during Friction Stir Welding, International Journal of Mechanical Engineering and Technology. 9 (8): 534–548.
Ikumapayi, O. M. and E. T. Akinlabi. (2019). Efficacy of Α-ꞵ Grade Titanium Alloy Powder (Ti-6Al-2Sn-2Zr-2Mo-2Cr-0.25Si) in Surface Modification and Corrosion Mitigation in 3.5 % Nacl on Friction Stir Processed Armour Grade 7075-T651 Aluminium Alloys – Insight in Defence Applications. Materials Research Express. 6 (7):1- 15.
Mulaba-Kapinga, D.; K. D. Nyembwe; O. M Ikumapayi, and E. T. Akinlabi (2020). Mechanical,
Electrochemical and Structural Characteristics of Friction Stir Spot Welds of Aluminium Alloy 6063. Manufacturing Review. 7 (25): 1-15.
Lokesh, S.; S. Bharat and K. S. Kuldeep. (2020). Manufacturing techniques for metal matrix composites (MMC): an overview, Advances in Materials and Processing Technologies. 6 (2): 441-457.
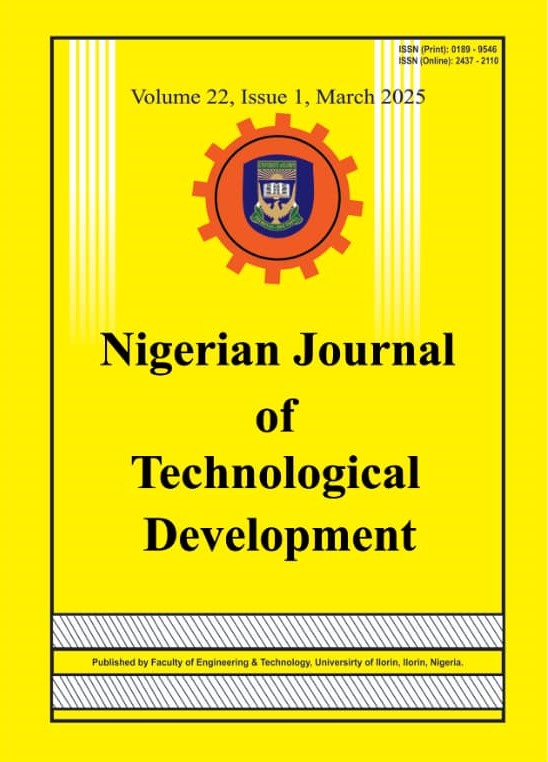
Downloads
Published
Issue
Section
License
Copyright (c) 2024 Nigerian Journal of Technological Development

This work is licensed under a Creative Commons Attribution-NonCommercial-ShareAlike 4.0 International License.
In accordance with the Copyright Act of 1976, which became effective January 1, 1978, the following statement signed by each author must accompany the manuscript submitted: "I, the undersigned author, transfer all copyright ownership of the manuscript referenced above to the Nigerian Journal of Technological Development, in the event the work is published. I warrant that the article is original, does not infringe upon any copyright or other proprietary right of any third party, is not under consideration by another journal, and has not been published previously. I have reviewed and approve the submitted version of the manuscript and agree to its publication in the Nigerian Journal of Technological Development." A copyright transfer form should be downloaded from the NJTD Website ( http://njtd.com.ng/index.php/njtd). Author(s) will be consulted, whenever possible, regarding republication of material. All authors must have access to the data presented and the authors and sponsor (if applicable) must agree to share original data with the editor if requested.