Enhancing Rice Milling Efficiency through Lean-Based Process Improvement Using Value Stream Mapping
DOI:
https://doi.org/10.63746/njtd.v22i3.3340Keywords:
Lean tools, Manufacturing value chain, Wastes, Value Stream MappingAbstract
Variability within a synchronous flow line due to process inefficiency and waste generation may jeopardise the production throughput. The study seeks to use a lean-based improvement process to enhance an existing rice processing and milling facility in Otukpo, Benue state, Nigeria, using a simulated model of Value Stream Mapping (VSM). The study objective is to appraise the state of the operations at various points in the manufacturing value chain using the existing state value stream map (ESVSM) and seek improvement where there are inefficiencies. The IGrafx software was employed in formulating and modeling the ESVSM, showing the process steps and identifying areas of waste on the processing line. Line balancing charts are drawn through simulation to identify imbalances in the process flow to optimise work flow at various workstations and increase process efficiency. Further analyses were conducted using the Monte Carlo sensitivity analysis on Python programmes to analyse the relationship between metrics such as productivity, quality, cost, and on-time delivery vis-à-vis other metrics such as cycle time, lead time, inventory, work-in-progress, finished goods, value-added time, production efficiency, defect rate, and on-time delivery. The results of the new state value stream map (NSVSM) present a reduction in the following areas: lead time by 61.24%, cycle time by 41.14%, raw material movement time by 64.44% and non-value added time by 90.08% with improvements in work in progress by 60.04% and overall process efficiency by 28.68% following the implementation of the lean tool. In addition, the simulation results show potential improvement in the overall production efficiency by 73.2%. This study may assist process industry in achieving process improvement. The novelty of this study lies in the fact that the development of a lean-based process for process improvement in rice milling operation using value stream mapping and simulation approach has not been sufficiently reported by the existing literature.
References
Abdulmalek, F. A. and Rajgopal, J. (2007). “Analyzing the Benefits of Lean Manufacturing and Value Stream Mapping via Simulation: A Process Sector Case Study.” International Journal of Production Economics, 107 (1): 223–236.
Adeodu, A. O., Maladzhi, R., Kana-kana Katumba, M. G. and I. A. Daniyan, I. A. (2023). Development of an improvement framework for warehouse processes using lean Six Sigma (DMAIC) approach: A case of third-party logistics (3PL) services. Heliyon, 9 (e14915):1-19.
Alves, A. C., Dinis?Carvalho, J. and Sousa, R. M. (2012). Lean production as promoter of thinkers to achieve companies' agility. The Learning Organization, 19, 219-237.
Bhasin, S. (2015). Lean Management beyond Manufacturing: A Holistic Approach. 1st Edition, Springer Cham, Switzerland, 2015. DOI: 10.1007/978-3-319-17410-5.
Bhasin, S. and Burcher, P. (2006). Lean viewed as a philosophy. J. Manuf. Technol. Manag. 17 (1) 56–72.
Black, J. and Black, J. R. (2008). Lean production: implementing a world-class system, Industrial Press Inc., Connecticut, US.
Cagliano, A. C., Grimaldis, S. and Schenone, M. (2018). Proposing a New Framework for Lean Warehousing: First Experimental Validation, vol. XXII, Summer School “Francesco Turco” – Industrial System Engineering, 2018.
Chizoba, B. O and Anugwu, C. C. (2022). Lean manufacturing approach and operational efficiency of Nigerian pharmaceutical companies in Anambra State. Saudi Journal of Business and Management Studies, 7(3): 94-99.
Ciarniene, R. and Vienažindiene, M. (2014). How to facilitate implementation of lean concept. Mediterranean Journal of Social Sciences, 5(13):177-183.
Daniyan, I. A. Adeodu, A. O., Mpofu, K., Maladhzi, R. and Kana-kana Katumba, M. G. (2022). Application of lean Six Sigma methodology using DMAIC approach for the improvement of bogie assembly process in the railcar industry” Heliyon, 8 (e09043):1-14.
De Treville, S. and Antonakis, J. (2009). Could lean production job design be intrinsically motivating? Contextual, configurational, and levels-of-analysis issues. Journal of Operations Management, 24(2): 99-123.
Díaz-Reza, J. R., García-Alcaraz, J., Marquez Figueroa, L., R. P. Vidal and Muro, J. (2022). Relationship between lean manufacturing tools and their sustainable economic benefits. The International Journal of Advanced Manufacturing Technology, 123:1269–1284, https://doi.org/10.1007/s00170-022-10208-0.
Henderson, B. A., Larco, J. L. and Martin, S. (1999). Lean Transformation: How to Change Your Business into a Lean Enterprise (Richmond, VA).
Hines, P., Holweg, M. and Rich, N. (2004). “Learning to evolve – a review of contemporary lean thinking. International Journal of Operations & Production Management, 24(10): 994-1011, 2004.
Holweg, H. (2007). The genealogy of lean production. Journal of Operations Management, 25(1)420-437.
Ikumapayi, O., Akinlabi, E., Mwema, F. and Ogbonna, O. (2020). Six sigma versus lean manufacturing–An overview. Materials Today: Proceedings, 26, 3275-3281.
Jaiprakash, B. and Sangwan, K. S. (2014). Lean manufacturing: Literature review and research issues. International Journal of Operations & Production Management 34(7):876-940.
Kafuku, J. M. (2019). Factors for effective implementation of lean manufacturing practice in selected industries in Tanzania. Procedia Manufacturing 33:351-358.
King, A. A. and Lenox, M. J. (2002). Lean and green? An empirical examination of the relationship between lean production and environmental performance. Production and operations management, 10, 244-256.
King, P. L. (2009). Lean in the process industries: dealing with complexities. Taylor & Francis Group 270 Madison Avenue New York, NY Productivity Press 10016, 2009.
KPMG, “Rice Industry Review,” (2019). pp. 40, [Online]. Available: https://assets.kpmg/conten t/dam/kpmg/ng/pdf/audit/rice-industry-review. pdf. Retrieved: 17th April, 2022.
Liker, J. K. and Morgan, J. M. (2006). The Toyota way in services: the case of lean product development. Academy of management perspectives, 20, 5-20.
Lyons, A. C., Vidamour, K., Jain, R. and Sutherland, M (2013). “Developing an understanding of lean thinking in process industries; Production planning & control” The Management of Operations; 24 (6):1-20.
Magodi, Y., Daniyan, I. A. and Mpofu, K. (2022a). An investigation of the effect of the ISO 9001 quality management system on small and medium enterprises in Gauteng, South Africa. South African Journal of Industrial Engineering, 33(1):126-138.
Magodi, Y., Daniyan, I. A. and Mpofu, K. (2022b). Application of lean six sigma to a small enterprise in the Gauteng province: A case study. South African Journal of Industrial Engineering, 33(1):190-204.
Marodin, G. A., Tortorella, G. L., Frank, A. G. and Godinho Filho, M. (2017). The moderating effect of Lean supply chain management on the impact of Lean shop floor practices on quality and inventory.Supply Chain Manag.: Int. J. 22 (6):473–485.
Maware, C., Okwu, M. O. & Adetunji, O. A. (2020). “Systematic literature review of lean manufacturing implementation in manufacturing-based sectors of the developing and developed countries”. International Journal of Lean Six Sigma, 13(3): 521–556.
Melton, T. (2005). The benefits of lean manufacturing: what lean thinking has to offer the process industries. Chemical engineering research and design, 83, 662-673.
Nwanya, S. C. and Oko, A. O. (2019). “The limitations and opportunities to use lean based continuous process management techniques in Nigerian manufacturing industries – a review” presented at the International Conference on Engineering for Sustainable World; Journal of Physics” Conference Series 1378.
?hno. T. (1988). “Toyota Production System: Beyond Large-Scale Production”. Productivity Press, New York.
Oko, A. and Kang, P. (2015). Lean six sigma approach to improve the admissions process for a Nigerian HE Institute. International Journal of Scientific and Engineering Research, 6(15): 368-378.
Okocha, O. L. and Wan Daud W N (2021). Conceptual issues to relevancy of adopting lean production in Nigerian manufacturing companies. International Journal of Academic Research in Accounting Finance and Management Sciences, 11(4), 99-114, 2021.
Oladipupo, O., Adeyinka, A. M. and O. Durodola (2023). Exploring lean six sigma: A comprehensive review of methodology and its role in business improvement” International Journal of Multidisciplinary Research and Growth Evaluation. 4(6):939-947.
Olu-Lawal, K. A., Ekemezie, I. O. and Usiagu, G. S. (2024). Lean manufacturing in industrial engineering: A USA and African review” GSC Advanced Research and Reviews, 18(02), 225–233.
Panwar, A., Nepal, B., Jain, R. and Lyons, A. (2017). Understanding the linkages between lean practices and
performance improvements in Indian process industries. Industrial Management & Data Systems 117(2):346-364.
Roriz, C., Nunes, E. and Sousa, S. (2017). Application of lean production principles and tools for quality improvement of production process in a cartoon company. Procedia Manuf. 11:1069–1076.
Shah, R. and Ward, P. T. (2007). Defining and developing measures of lean production. Journal of Operations Management, 25(1):785-805, 2007.
Sunder, M. V. and Antony, J. (2018). A conceptual Lean Six Sigma framework for quality excellence in higher education institutions. Int. J. Qual. Reliab. Manag. 35 (4): 857–874.
Sunder, M. V. and Mahalingam, S. (2018). An empirical investigation of implementing lean six sigma in higher education institutions. Int. J. Qual. Reliab. Manag. 35 (10):2157–2180.
Sunder, M. V., Ganesh, L. S. and Marathe, R. R. (2019). Lean six sigma in consumer banking: an empirical inquiry. Int. J. Qual. Reliab. Manag. 36 (8):1345–1369.
Sutrisno, A., Vanany, I., Gunawan, I. and Asjad, M. (2018). Lean waste classification model to support the sustainable operational practice. IOP Conference Series: Materials Science and Engineering, 337 012067.
Tohidi, H. and Khedriliraviasl, K (2012). Six sigma methodology and its relationship with lean manufacturing system. Advances in Environmental Biology, 6, 895-906.
Tortorella, G. L., Miorando, R. and Tlapa, D. (2017). Implementation of lean supply chain: an empirical research on the effect of context. The TQM J. 29 (4):610–623.
Vinodh, S., Arvind, K. and Somanaathan, M. (2011). Tools and techniques for enabling sustainability through lean initiatives. Clean Technologies and Environmental Policy, 13, 469-479.
Womarck, J. P., Jones, D. T. and Roos, D. (2004). The Machine that changed the World. 11th edition, New York, Maxwell Macmilla.
Xia, W. and Sun, J. (2013). Simulation guided value stream mapping and lean improvement: A case study of a tubular machining facility. Journal of Industrial Engineering and Management, 6(2): 456-476 2013.
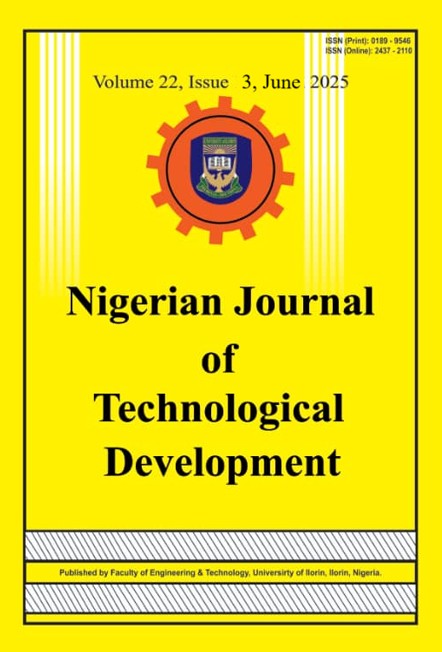
Downloads
Published
Issue
Section
License
Copyright (c) 2025 Nigerian Journal of Technological Development

This work is licensed under a Creative Commons Attribution-NonCommercial-ShareAlike 4.0 International License.
In accordance with the Copyright Act of 1976, which became effective January 1, 1978, the following statement signed by each author must accompany the manuscript submitted: "I, the undersigned author, transfer all copyright ownership of the manuscript referenced above to the Nigerian Journal of Technological Development, in the event the work is published. I warrant that the article is original, does not infringe upon any copyright or other proprietary right of any third party, is not under consideration by another journal, and has not been published previously. I have reviewed and approved the submitted version of the manuscript and agree to its publication in the Nigerian Journal of Technological Development." A copyright transfer form can be downloaded from the NJTD Website (http://njtd.com.ng/index.php/njtd). Author(s) will be consulted, whenever possible, regarding republication of material. All authors must have access to the data presented, and the authors and sponsor (if applicable) must agree to share original data with the editor if requested.