Characterization And Impact Of Cutting Parameters On Face-Milled Surfaces Of Pearlitic Ductile Iron
DOI:
https://doi.org/10.63746/njtd.v21i2.2350Keywords:
Cutting characterization, Cutting parameters, Face milling, Dry cutting, Pearlitic ductile iron, Roughness characteristicsAbstract
In an attempt to enhance the surface integrity of machined parts in the manufacturing industries, face-milled surface profiles of pearlitic ductile iron were characterized and analysed based on the effects of some cutting parameters. The pearlitic ductile iron used was locally prepared. Atomic Force Microscope and Scanning Electron Microscope were used to characterizing the roughness profile of the machined workpiece. The results showed increase in depth of cut from 400.37 to 652.37 nm at constant cutting fluid flow rate, cutting speed and feed rate. Also, at varying cutting fluid flow rate, the roughness parameter decreased from 733.56 to 272.84 nm at constant feed rate, depth of cut and cutting speed. Similar result was obtained with varying feed rate. However, there exists no definable course as cutting speed increases at constant cutting fluid flow rate, depth of cut and feed rate. In conclusion, it was found that machining at cutting fluid flow rate of 4 l/min, feed rate of 30 mm/rev, depth of cut of 0.2 mm and cutting speed of 1000 rev/min produced better quality surfaces. Therefore, the findings in this study will be useful for the manufacturing industries to improve on the surface reliability of the face milling process.
References
Abiodun, M. O.; O. O. Ilori and K. M. Adeleke. (2018). Effect of Maize-Starch Based Cutting Fluids and Machining Parameters on Temperature Generated in Turning of AISI 304 Stainless Steel. International Journal of Multidisciplinary Sciences and Engineering, 9 (6): 18–23.
Arunachalam, R. M.; M. A. Mannan and A. C. Spowage. (2004). Residual Stress and Surface Roughness When Facing Age Hardened Inconel 718 with CBN and Ceramic Cutting Tools. International Journal of Machine Tools and Manufacture, 44: 879–887.
Bembenek, M.; D. Dzienniak; A. Dzindziora; M. Sułowski and L. Ropyak. (2023). Investigation of the Impact of Selected Face Milling Parameters on the Roughness of the Machined Surface for 1.4301 Steel. Advances in Science and Technology Research Journal, 17(4): 299–312.
Ezugwu, E. O.; A. Richetti; A. R. Machado; M. B. Da Silva and J. Bonney. (2004). Influence of the Number of Inserts for Tool Life Evaluation in Face Milling of Steels. International Journal of Machine Tools and Manufacture, 44(7-8): 695–700.
Grzesik, W. and Wanat, T. (2005). Comparative Assessment of Surface Roughness Produced by Hard Machining with Mixed Ceramic Tools Including 2D and 3D Analysis. Journal of Materials Processing Technology, 169: 364–371.
Grzesik, W. and Zak, K. (2012). Surface Integrity Generated by Oblique Machining of Steel and Iron Parts. Journal of Materials Processing Technology, 212: 2586–2596.
Gunnberg, F.; M. Escursell and M. Jacobson. (2006). The Influence of Cutting Parameters on Residual Stresses and Surface Topography During Hard Turning of 18MnCr5 Case Carburized Steel. Journal of Materials Processing Technology, 174: 82–90.
Hayajneh, M. T.; M. S. Tahat and J. Bluhm. (2007). A Study of the Effects of Machining Parameters on the Surface Roughness in the End-Milling Process. Jordan Journal of Mechanical and Industrial Engineering, 1(1): 1– 5.
Jacobson, M.; P. Dahlman and F. Gunnberg. (2002). Cutting Speed Influence on Surface Integrity of Hard Turned Bainite Steel. Journal of Materials Processing Technology 128: 318–323.
Kuram, E.; B. Ozcelik; E. Demirbas and E. Şık. (2010). Effects of the Cutting Fluid Types and Cutting Parameters on Surface Roughness and Thrust Force. Proceedings of the World Congress on Engineering Volume II, June 30 - July 2, London, U.K.
Ilori, O. O.; D. A. Adetan and L. E. Umoru. (2016). Effect of Cutting Parameters on the Surface Roughness Generated during Face Milling Operation of Pearlitic Ductile Iron with Cemented Carbide Tool. Acta Technica Corviniensis-Bulletin of Engineering Tome IX, 4: 137-144.
Ilori, O. O.; D. A. Adetan and L. E. Umoru. (2017). Effect of Cutting Parameters on the Surface Residual Stress of Face-Milled Pearlitic Ductile Iron. International Journal of Materials Forming and Machining Processes, 4 (1): 38-52.
llori, O. O.; K. M. Adeleke; M. O. Abiodun and I. A. Idowu. (2018). Maize-Starch Based Cutting Fluids and Process Parameters Influence on Cutting Force in Turning of AISI 304 Stainless Steel. Journal of Nigeria Institute of Mechanical Engineering, 8 (2): 102-110.
Isik, Y. (2007). Investigating the Machinability of Tool Steels in Turning Operations. Materials and Design, 28(5): 1417–1424.
Rech, J. and Moisan, A. (2003). Surface Integrity in Finish Hard Turning of Case Hardened Steels. International Journal of Machine Tools and Manufacture, 43: 543–550.
Sosa, A. D.; M. D. Echeverri; O. J. Moncada and J. A. Sikora. (2007). Residual Stresses, Distortion and Surface Roughness Produced by Grinding Thin Wall Ductile Iron Plates. International Journal of Machine Tools and Manufacture, 47: 229–235.
Thiele, J. D. and Melkote, S. N. (1999). Effect of Cutting Edge Geometry and Workpiece Hardness on Surface Generation in the Finish Hard Turning of AISI 52100 Steel. Journal of Materials Processing Technology, 94: 216 – 226.
Uyaner, M.; A. Akdemir; S. Yazman and H. Saglam. (2012). The Effects of Cutting Speed and Depth of Cut on Machinability Characteristics of Austempered Ductile Iron. Journal of manufacturing science and engineering, 134 (2): 10-13.
Yusuf, K.; Y. Nukman; T. M. Yusof; S. Z. Dawal; H. Q. Yang; T. M. I. Mahlia and K. F. Tamrin. (2010). Effect of Cutting Parameters on the Surface Roughness of Titanium Alloys Using End Milling Process. Scientific Research and Essays, 5(11): 1284-1293.
Zhou, J. M.; V. Bushlya and J. E. Stahl. (2012). An Investigation of Surface Damage in the High Speed Turning of Inconel 718 with Use of Whisker Reinforced Ceramic Tools. Journal of Materials Processing Technology, 212: 372– 384.
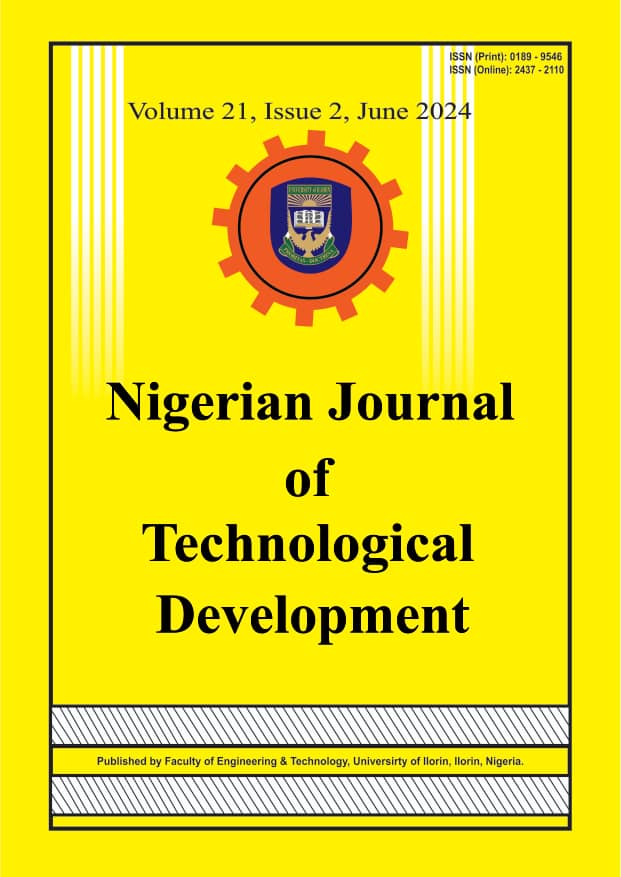
Downloads
Published
Issue
Section
License
Copyright (c) 2024 Nigerian Journal of Technological Development

This work is licensed under a Creative Commons Attribution-NonCommercial-ShareAlike 4.0 International License.
In accordance with the Copyright Act of 1976, which became effective January 1, 1978, the following statement signed by each author must accompany the manuscript submitted: "I, the undersigned author, transfer all copyright ownership of the manuscript referenced above to the Nigerian Journal of Technological Development, in the event the work is published. I warrant that the article is original, does not infringe upon any copyright or other proprietary right of any third party, is not under consideration by another journal, and has not been published previously. I have reviewed and approved the submitted version of the manuscript and agree to its publication in the Nigerian Journal of Technological Development." A copyright transfer form can be downloaded from the NJTD Website (http://njtd.com.ng/index.php/njtd). Author(s) will be consulted, whenever possible, regarding republication of material. All authors must have access to the data presented, and the authors and sponsor (if applicable) must agree to share original data with the editor if requested.