Mould Design Improvement and Flaw Analysis for Investment Casting Process using Numerical Computation with Experimental Validation
DOI:
https://doi.org/10.63746/njtd.v22i1.2910Keywords:
Altair Inspire Cast, Cold shut, Investment casting, Optimization, Shrinkage porosityAbstract
Investment casting is recognized for producing intricate shapes in a single process, eliminating the need for multiple manufacturing and assembly processes for welding and bending. However, challenges remain where flaws, such as shrinkage porosity can affect product quality. This research uses numerical simulations using Altair Inspire Cast to minimize flaws in the investment casting process for vehicle barrier support components made from stainless steel 304. This study begins with a numerical simulation of an existing mould design based on actual process parameters, followed by an experimental investigation of flaw occurrence and location. Several casting designs were tested, analyzing liquid metal behavior during filling and solidification. The initial design of Case 1a showed 455 mm³ of shrinkage volume, which was eliminated by rotating the casting parts 90 degrees in Case 1b. A further design improvement in Case 2a increased the casting yield by over 10% by reducing 50% the gating system height. However, without optimal parameters, cold shuts were introduced. Case 2b, which uses a shorter filling time of 10 seconds successfully mitigates the cold shut. Final design modifications (Case 3) were validated through actual fabrication, showing that flaw location could be predicted and process optimization achieved for higher-quality products.
References
Ahmad, S. N., Manurung, Y. H., Adenan, M. S., Yusof, F., Mat, M. F., Prajadhiana, K. P., Minggu, Z., Leitner, M., & Saidin, S. (2022). Experimental validation of numerical simulation on deformation behaviour induced by wire arc additive manufacturing with feedstock SS316L on substrate S235. International Journal of Advanced Manufacturing Technology, 119(3–4), 1951–1964.
Borikar, V. N., Kapgate, P. G., Wairagade, R. A., & Kshirsagar, A. D. (2017). Optimization of Casting Components by Minimizing Cold Shut Defect. 5(3), 3–5.
Bruna, M., Bolibruchová, D., PastirÄák, R., & RemiÅ¡ová, A. (2019). Gating System Design Optimization for Investment Casting Process. Journal of Materials Engineering and Performance, 28(7), 3887–3893.
Carlson, K. D., Ou, S., Hardin, R. A., & Beckermann, C (2002). Development of new feeding-distance rules using casting simulation: Part I. Methodology. Metallurgical and Materials Transactions B: Process Metallurgy and Materials Processing Science, 33(5), 731–740.
Choe, C. M., Yang, W. C., Kim, U. H., Ri, B. G., & Om, M. S. (2022). Manufacture of centrifugal compressor impeller using FDM and investment casting. International Journal of Advanced Manufacturing Technology, 118(1–2), 173–181.
Condruz, M. R., & Badea, T. A. (2021). Computational And Experimental Study On Defect Emergence In Computational And Experimental Study On Defect Emergence In Investment Cast. January.
Feng, Y., Liao, D., & Chen, T. (2021). Confluence And Cold Shut Computation Based On Time Field In Casting Simulation. 18(2), 101–109.
Fu, M. W., & Yong, M. S. (2009). Simulation-Enabled Casting Product Defect Prediction In Die Casting Process. International Journal Of Production Research, 47(18), 5203–5216.
Hao, X., Liu, G. Huai, Wang, Y., Wu, S. Ping, & Wang, Z. Dong. (2022). Optimization Of Investment Casting Process For K477 Superalloy Aero-Engine Turbine Nozzle By Simulation And Experiment. China Foundry, 19(4), 351–358.
Jadhav, R., & Mane, V. (2020). Design And Analysis Of Gating System At Various Orientation For Rear Break Drum By Using Casting Simulation Software. 2.
Jones, C. A., Jolly, M. R. ., Jarfors, A. E. W., Irwin, M., Svenningsson, R., Steggo, J., & Eriksson, J. (2020). A Verification Of Thermophysical Properties Of A Porous Ceramic Investment Casting Mould Using Commercial Computational Fluid Dynamics Software. Iop Conference Series: Materials Science And Engineering, 861(1).
Khalajzadeh, V., & Beckermann, C. (2020). Simulation Of Shrinkage Porosity Formation During Alloy Solidification. Metallurgical And Materials Transactions A: Physical Metallurgy And Materials Science, 51(5), 2239–2254.
Khan, M. A. A., & Sheikh, A. K. (2018). A Comparative Study Of Simulation Software For Modelling Metal Casting Processes. International Journal Of Simulation Modelling, 17(2), 197–209.
Kumar, V., Ali, B., & Khan, N. (2018). Analysis Casting Simulation And Its Importance. Iosr Journal Of Engineering (Iosrjen), 08(6), 72–82. Www.Iosrjen.Org
Kuo, J. K., Huang, P. H., Lai, H. Y., & Chen, J. R. (2017). Optimal Gating System Design For Investment Casting Of 17-4ph Stainless Steel Enclosed Impeller By Numerical Simulation And Experimental Verification. International Journal Of Advanced Manufacturing Technology, 92(1–4), 1093–1103.
Li, F., Wang, Y., Wang, D., & Zhao, Y. (2021). Comparison Of Various Gating Systems For Investment Casting Of Hydraulic Retarder Impeller With Complex Geometry. 235(4), 583–593
Liu, Y., He, H., Gao, J., Li, G., Liang, Y., & Li, L. (2022). Research On The Low-Pressure Casting Process Of A Double Suction Impeller In 304 Austenitic Stainless Steel With High Performance And Thin-Wall Complex Structure. Journal Of Physics: Conference Series, 2390(1).
Malik, I., Sani, A. A., & Medi, A. (2020). Study On Using Casting Simulation Software For Design And Analysis Of Riser Shapes In A Solidifying Casting Component. Journal Of Physics: Conference Series, 1500(1).
Mat, M. F., Manurung, Y. H. P., Muhammad, N., Ditler, A., Abd Ghani, M. S., & Leitner, M. (2020). Grain Growth Prediction Of Bead-On-Plate With Filler Wire Ss316l Using Fem. Iop Conference Series: Materials Science And Engineering, 834(1).
Precision Forming Technology Of Large Superalloy Castings For Aircraft Engines. (N.D.).
Rafique, M. M. A., & Iqbal, J. (2009). Modeling And Simulation Of Heat Transfer Phenomena During Investment Casting. International Journal Of Heat And Mass Transfer, 52(7–8), 2132–2139.
Rajaram, D., Sooriyamoorthy, E., & Sankaranarayanan, A. K. (2024). Automated Optimization Of Gating System Through Numerical Simulation. Proceedings Of The Institution Of Mechanical Engineers, Part B: Journal Of Engineering Manufacture.
Raza, M., Irwin, M., & Fagerström, B. (2015). The Effect Of Shell Thickness, Insulation And Casting Temperature On Defects Formation During Investment Casting Of Ni-Base Turbine Blades. Archives Of Foundry Engineering, 15(4), 115–123.
Å abÃk, V., Futáš, P., Pribulová, A., & Delimanová, P. (2021). Optimization Of A Gating System By Means Of Simulation Software To Eliminate Cold Shut Defects In Casting. 5(1), 1–4.
Wang, D., Dong, A., Zhu, G., Shu, D., Sun, J., Li, F., & Sun, B. (2018). Rapid Casting Of Complex Impeller Based On 3d Printing Wax Pattern And Simulation Optimization.
Wang, X., & Zhang, Z. (2011). Simulation Of Flow Field And Temperature Tield In The Process Of Filling And Solidification For K424 Alloy Thin-Walled Casting. 68, 1568–1573.
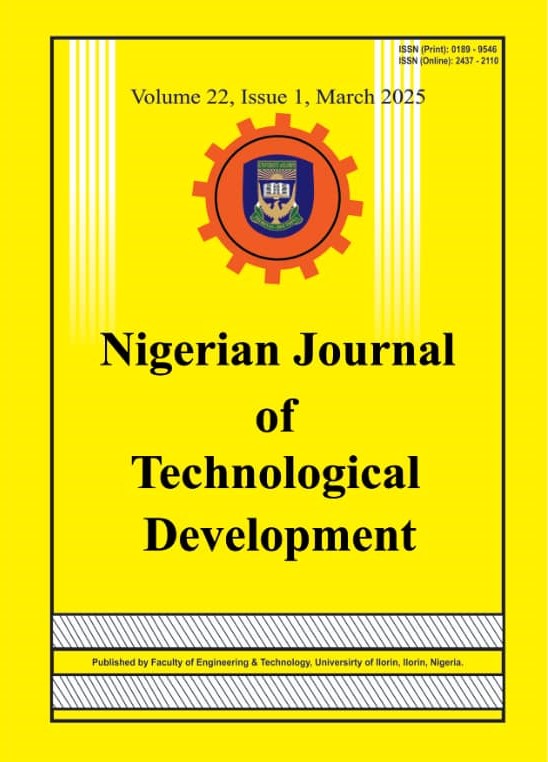
Downloads
Published
Issue
Section
License
Copyright (c) 2025 Nigerian Journal of Technological Development

This work is licensed under a Creative Commons Attribution-NonCommercial-ShareAlike 4.0 International License.
In accordance with the Copyright Act of 1976, which became effective January 1, 1978, the following statement signed by each author must accompany the manuscript submitted: "I, the undersigned author, transfer all copyright ownership of the manuscript referenced above to the Nigerian Journal of Technological Development, in the event the work is published. I warrant that the article is original, does not infringe upon any copyright or other proprietary right of any third party, is not under consideration by another journal, and has not been published previously. I have reviewed and approve the submitted version of the manuscript and agree to its publication in the Nigerian Journal of Technological Development." A copyright transfer form should be downloaded from the NJTD Website ( http://njtd.com.ng/index.php/njtd). Author(s) will be consulted, whenever possible, regarding republication of material. All authors must have access to the data presented and the authors and sponsor (if applicable) must agree to share original data with the editor if requested.