A Hybrid Method for Identifying Critical Failure Modes in a Ball Mill
DOI:
https://doi.org/10.63746/njtd.v21i3.2696Keywords:
FMEA, FMECA, COPRAS-G, Reliability Engineering, Mineral ProcessingAbstract
The reliability of a ball mill is crucial for the seamless operation of ore processing and other industrial plants, where unexpected equipment failure or downtime can result in significant financial losses and reduced production efficiency. Thus, this paper examined a hybrid method for identifying critical failure modes in a ball mill using the Failure Modes, Effects, and Criticality Analysis combined with the Complex Proportional Assessment with
Grey Numbers (COPRAS-G). The COPRAS-G method was employed to assess the criticality of various failure modes by determining the weights of significant failure modes in the bearing, gearbox, motor, and shaft components of a ball mill. It was observed that gear seal failure is the most critical failure with percentage contribution (Ni) of 100%, while bearing wear is the least critical failure with percentage contribution (Ni) of 62%. The result suggests that failure
modes of gear seal failure, gear pitting, motor bearing fatigue, and shaft fracture are regarded as the main contributors to failure with percentage contribution (Ni) of 100%, 97%, 87% and 83% respectively. Current ball mill maintenance includes corrective, preventive and predictive maintenance. For failure modes with high criticality, predictive maintenance was advised, while for moderate and low criticality, corrective and preventive maintenance were advised.
References
Adhikary, D.; G. K. Bose; D. Bose. and S. Mitra. (2014). ‘Multi criteria FMECA for coal-fired thermal power plants using COPRAS-G’, International Journal of Quality and Reliability Management, 31(5), pp. 601–614.
Aghdaie, M. H., S. H. Zolfani and E. K. Zavadskas. (2013). 'Decision making in machine tool selection: An integrated approach with SWARA and COPRAS-G methods', Engineering Economics, 24(1), pp. 52-64.
Bowles, J. B. and Peldez, E. C. (1995). Fuzzy logic prioritization of failures in a system failure mode, effects and criticality analysis, Reliability Engineering and System Safety.
Byiringiro, J., J. K. Kimotho; M. K. Ndeto and H. M. Ndiritu. (2020). 'Dynamic structural analysis of a small-scale ball mill using Ansys and EDEM', Journal of Sustainable Research in Engineering, 4(3), pp. 99-110.
Chang, K. H.; Y. C. Chang and Y. T. Lee. (2014). ‘Integrating TOPSIS and DEMATEL methods to rank the risk of failure of FMEA’, International Journal of Information Technology and Decision Making, 13(6), pp. 1229–1257.
Cristea, G. and Constantinescu, D. M. (2017). ‘A comparative critical study between FMEA and FTA risk analysis methods’, in IOP Conference Series: Materials Science and Engineering. Institute of Physics Publishing.
Dabbagh, R. and Yousefi, S. (2019). ‘A hybrid decision-making approach based on FCM and MOORA for occupational health and safety risk analysis’, Journal of Safety Research, 71, pp. 111–123. Available at: https://doi.org/10.1016/j.jsr.2019.09.021.
Dinmohammadi, F.; B. Alkali; M. Shafiee; C. Berenguer and A. Labib. (2016). ‘Risk Evaluation of Railway Rolling Stock Failures Using FMECA Technique: A Case Study of Passenger Door System’, Urban Rail Transit, 2(3–4), pp. 128–145.
Jun, L. and Huibin, X. (2012). ‘Reliability analysis of aircraft equipment based on FMECA method', Physics Procedia, 25, pp. 1816–1822.
Kim, K. O. and Zuo, M. J. (2018). ‘General model for the risk priority number in failure mode and effects analysis’, Reliability Engineering and System Safety, 169, pp. 321–329.
Kimura, M.; M. Narumi and T. Kobayashi. (2007). 'Design method of ball mill by discrete element method', Sumitomo Kagaku, (2007-II), pp. 1-6.
Kiran, M. B. (2022). 'A Review of Failure Mode Effect and Criticality Analysis (FMECA)', Proceedings of the International Conference on Industrial Engineering and Operations Management, Istanbul, Turkey, March 7-10, 2022, IEOM Society International, pp. 4506-4510.
Liu, H. C.; L. Liu; Q. H. Bian; Q. L. Lin; P. C. Xu. (2011). ‘Failure mode and effects analysis using fuzzy evidential reasoning approach and grey theory’, Expert Systems with Applications, 38(4), pp. 4403–4415.
Liu, H. C.; J. X. You; X. Y. You and M. M. Shan. (2015). ‘A novel approach for failure mode and effects analysis using combination weighting and fuzzy VIKOR method’, Applied Soft Computing Journal, 28, pp. 579–588.
Lo, H.W. and Liou, J.J.H. (2018). ‘A novel multiple-criteria decision-making-based FMEA model for risk assessment’, Applied Soft Computing Journal, 73, pp. 684–696.
Nardo, D. M.; T. Murino; G. Osteria; L. C. Santillo. (2022). ‘A New Hybrid Dynamic FMECA with Decision-Making Methodology: A Case Study in an Agri-Food Company’, Applied System Innovation, 5(3).
Pancholi, N. and Bhatt, M. (2018). ‘FMECA-based maintenance planning through COPRAS-G and PSI’, Journal of Quality in Maintenance Engineering, 24(2), pp. 224–243.
Pancholi, N. and Bhatt, M. G. (2016). ‘Multicriteria FMECA Based Decision-Making for Aluminium Wire Process Rolling Mill through COPRAS-G’, Journal of Quality and Reliability Engineering, 2016. Available at: https://doi.org/10.1155/2016/8421916.
Sahoo, T.; P. K. Sarkar and A. K. Sarkar. (2008). Maintenance Optimization for Critical Equipments in process industries based on FMECA Method, Certified International Journal of Engineering and Innovative Technology (IJEIT).
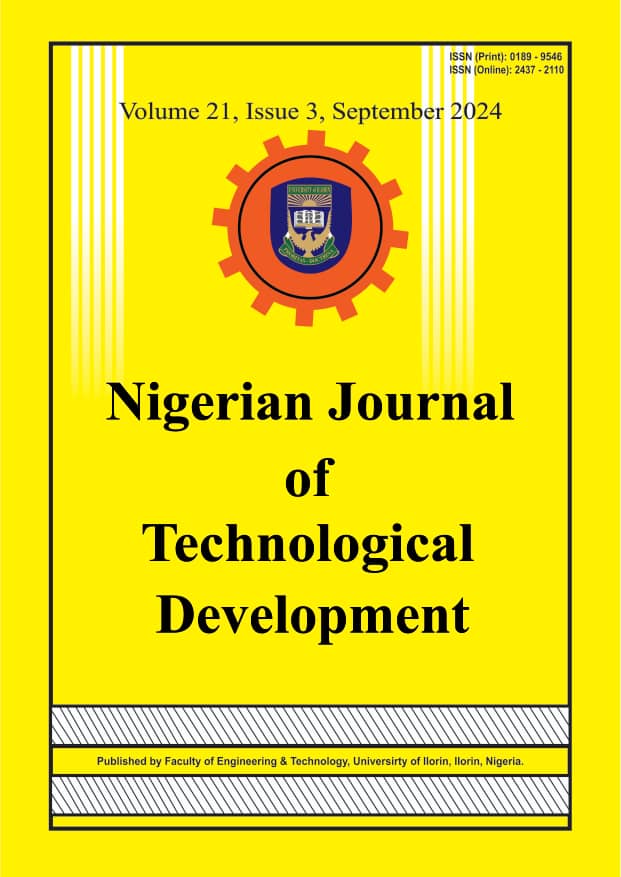
Downloads
Published
Issue
Section
License
Copyright (c) 2024 Nigerian Journal of Technological Development

This work is licensed under a Creative Commons Attribution-NonCommercial-ShareAlike 4.0 International License.
In accordance with the Copyright Act of 1976, which became effective January 1, 1978, the following statement signed by each author must accompany the manuscript submitted: "I, the undersigned author, transfer all copyright ownership of the manuscript referenced above to the Nigerian Journal of Technological Development, in the event the work is published. I warrant that the article is original, does not infringe upon any copyright or other proprietary right of any third party, is not under consideration by another journal, and has not been published previously. I have reviewed and approved the submitted version of the manuscript and agree to its publication in the Nigerian Journal of Technological Development." A copyright transfer form can be downloaded from the NJTD Website (http://njtd.com.ng/index.php/njtd). Author(s) will be consulted, whenever possible, regarding republication of material. All authors must have access to the data presented, and the authors and sponsor (if applicable) must agree to share original data with the editor if requested.